Frequent shutdown in the workshop? 90% of the reason is that the gas storage tank was not selected correctly! 3 minutes to learn about selection secrets, cost saving guide, and volume pressure ratio!
In the air compression system, the storage tank plays the core role of a "stabilizing reservoir" - it can buffer the pressure shock caused by gas volume fluctuations and store compressed air to meet peak demand, which is a key hub to ensure the efficient operation of the system.
Choosing a suitable gas storage tank requires a multiple balance between gas usage characteristics, system parameters, and safety standards.
The selection of air storage tanks, from small pneumatic tools in the workshop to centralized gas supply systems in large production lines, directly affects the energy consumption, stability, and service life of the entire compressed air system.
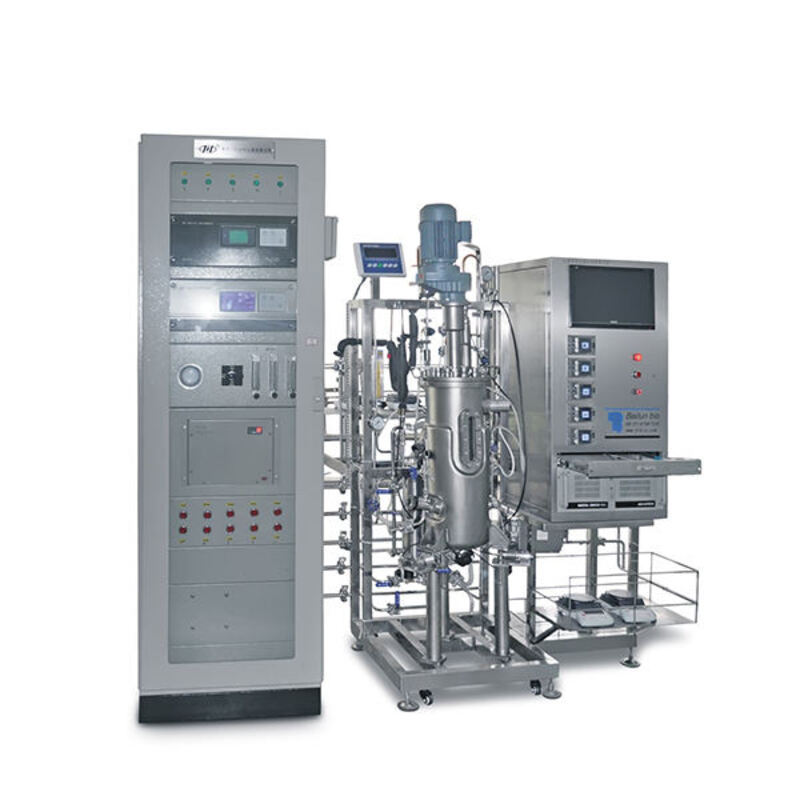
1、 Six principles of selection
The stability of the volume adapted gas volume is the core variable that determines the volume. When pneumatic equipment is frequently started and stopped or the gas consumption fluctuates rapidly, larger capacity air storage tanks can effectively smooth fluctuations - usually estimating the basic volume based on 1/3 to 1/5 of the air compressor displacement.
For example, an air compressor with a displacement of 10m ³/min is more suitable when paired with a 2-3.3m ³ air storage tank. But special attention should be paid to reserving expansion space: if there are plans to add new equipment in the future, it is recommended to increase the margin by 20% to 30% based on the calculated value to avoid repeated investment in the short term.
The rated working pressure of the pressure matching storage tank must match the exhaust pressure of the air compressor. If the exhaust pressure of the air compressor is 0.8 MPa, the rated pressure of the air storage tank should be selected as 1.0~1.2 MPa, which not only meets the pressure requirements of the gas equipment, but also reserves 10%~20% safety redundancy.
This type of matching not only avoids the risk of overpressure, but also reduces energy waste caused by pressure loss - data shows that systems with mismatched pressures consume 15% to 20% more energy than adaptive systems.
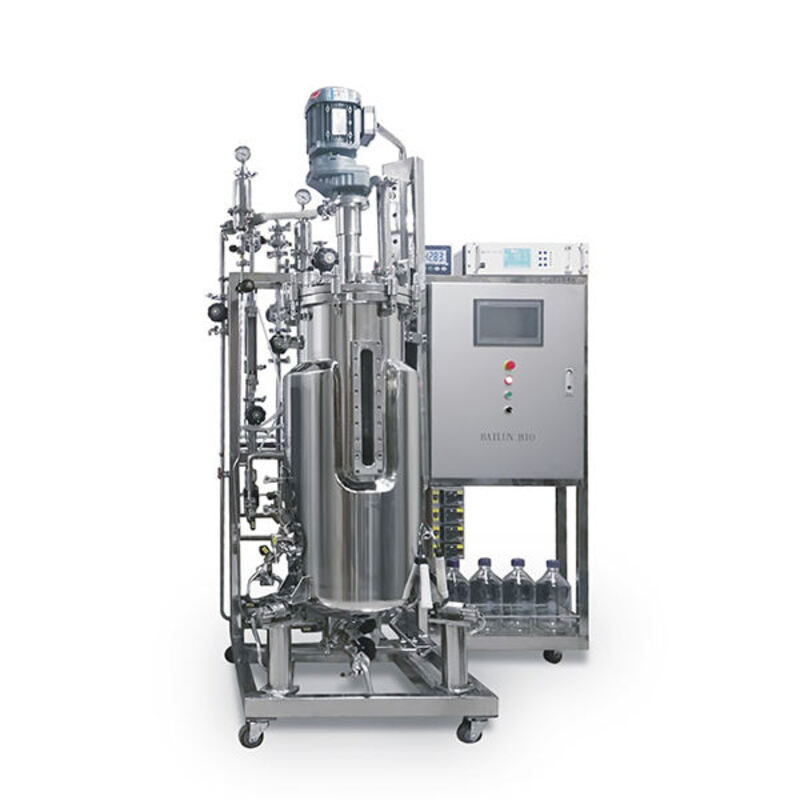
Material selection
The selection of carbon steel and stainless steel is essentially a mapping of scene requirements. Carbon steel gas storage tanks, with their advantages of high strength and low cost, have become the preferred choice for conventional industrial scenarios such as mechanical processing and building materials.
In fields such as food processing and pharmaceutical production that have strict requirements for air quality, the corrosion resistance of stainless steel gas storage tanks is crucial - their surface smoothness can reduce microbial growth and resist corrosion caused by condensed water in compressed air, extending their service life by 3-5 years compared to carbon steel tanks.
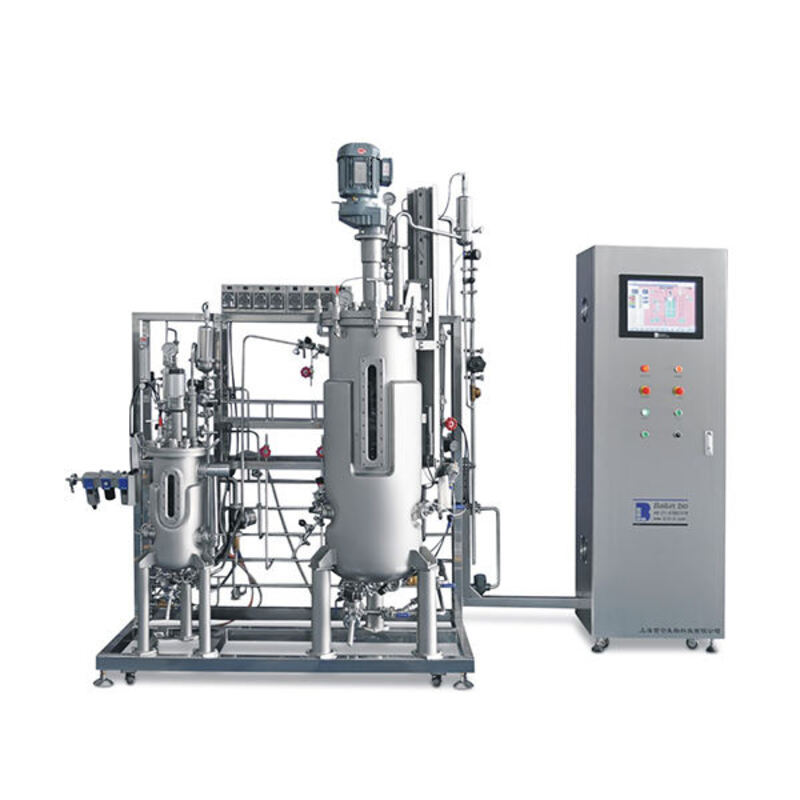
Installation method
The choice between vertical and horizontal requires careful consideration. The vertical gas storage tank occupies only one-third of the horizontal area and is suitable for small spaces such as workshop corners. However, its height is relatively high (usually 3-5 meters), and a top maintenance space needs to be reserved.
Horizontal gas storage tanks have better stability, especially suitable for sites with limited foundation bearing capacity, but their length can reach 6-10 meters, and it is necessary to ensure that there is a maintenance channel of more than 1.5 meters around them. In special scenarios, underground installation (requiring anti-corrosion treatment) can also be used to further save ground space.
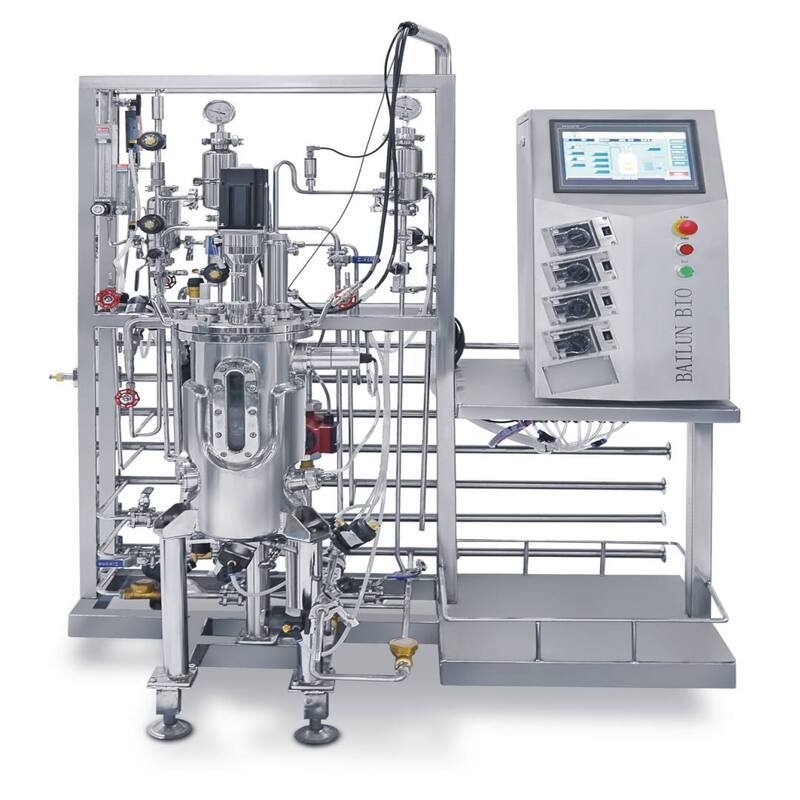
Interface compatibility
The interface size and quantity need to be carefully calculated. A diameter that is too small can lead to pressure loss, while a diameter that is too large can increase costs. Generally, it should be consistent with the outlet diameter of the air compressor and the inlet diameter of the dryer (such as DN50, DN80, etc.).
The number of interfaces should be based on the configuration of the auxiliary equipment: at least interfaces for safety valves, pressure gauges, and drain valves should be reserved. If multiple gas consuming devices need to be connected, branch interfaces can be added, but attention should be paid to symmetrical arrangement to reduce airflow disturbance.
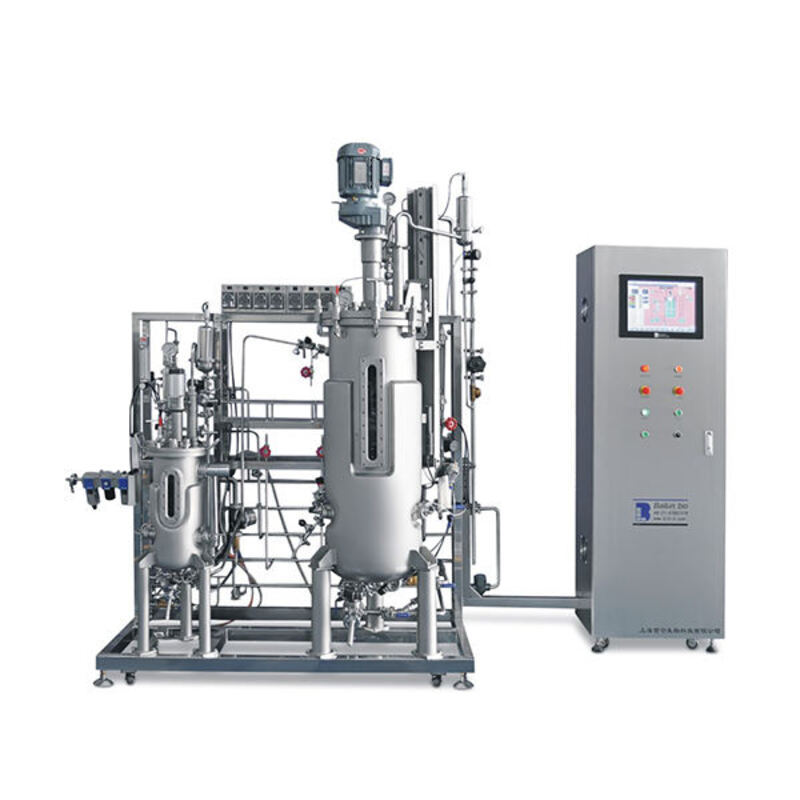
Safety net
The gas storage tank must be equipped with a verified safety valve (with a popping pressure not exceeding 1.05 times the rated pressure), a pressure gauge with an accuracy level not lower than 1.6, and the body must comply with the GB150 "Pressure Vessels" standard, and have a complete factory certificate and supervision certificate.
Regular inspection is equally crucial - an external inspection must be conducted annually, and a hydrostatic test must be conducted every three years to ensure that the tank is free from safety hazards such as cracks and corrosion.
2、 Volume Calculation: From Empirical Estimation to Accurate Quantification
When the gas usage scenario is complex or requires high accuracy, relying solely on empirical estimation is difficult to meet the requirements. In this case, precise calculations need to be made using formulas, and the two core formulas cover different working conditions.
Formula 1: Dynamic balance calculation based on air compressor parameters is suitable for scenarios with clear gas fluctuation characteristics. The formula is: V=N × Q ÷ (P+1)
Among them: V is the volume of the gas storage tank (m ³); Q is the displacement of the air compressor (m ³/min); P is the exhaust pressure (MPa); N is the coefficient of fluctuation (1-2 for stable operating conditions, 3 for general fluctuations, and 4 or more for severe fluctuations).
Case: A certain automotive parts factory's air compressor has a displacement of 20m ³/min and an exhaust pressure of 0.7MPa. The gas used in the production line fluctuates violently due to frequent mold changes (N=4).
Calculated as V=4 × 20 ÷ (0.7+1) ≈ 47m ³, considering the addition of 2 welding robots in the future, a 50m ³ gas storage tank is ultimately chosen.
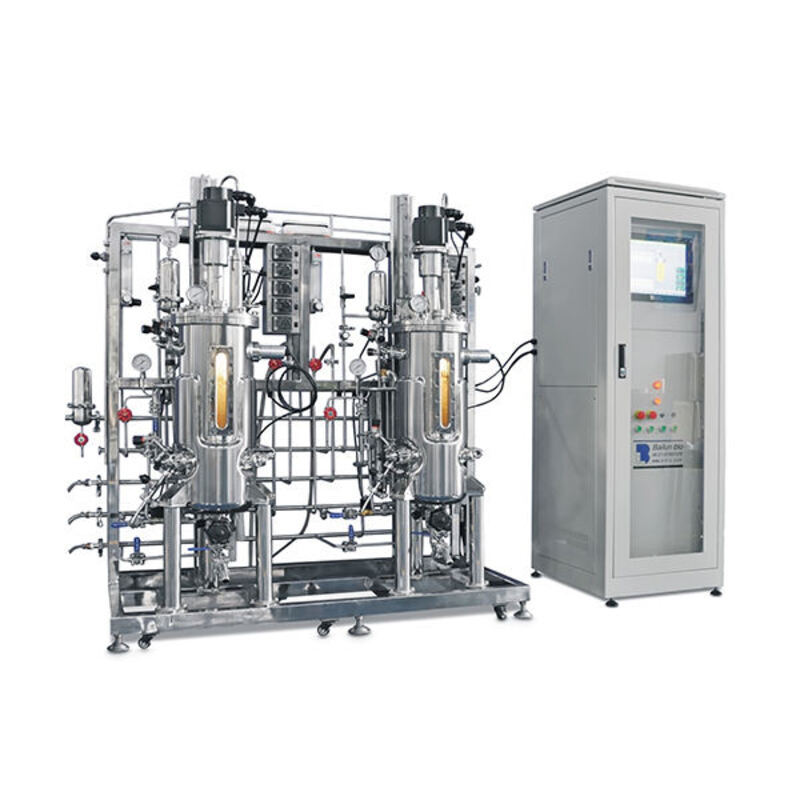
Formula 2: Static reserve calculation based on gas source guarantee time
Applicable to scenarios where continuous gas supply is required in case of sudden gas interruption, the formula is: V=Qs × t × P0 ÷ (P1-P2)
Among them: V is the volume of the gas storage tank (m ³); Qs is the design capacity of the gas source (Nm ³/min, flow rate under standard conditions);
To ensure time (min, usually 5-20 min, critical processes can be extended to 30 min); P0 is atmospheric pressure (101.33kPa); P1 is the normal working pressure (kPa); P2 is the minimum allowable pressure (kPa).
Case: A certain electronic factory's gas source design capacity is 15Nm ³/min, with a normal working pressure of 900kPa and a minimum allowable pressure of 700kPa. It is required to ensure gas supply for 15 minutes after gas interruption.
Calculated: V=15 × 15 × 101.33 ÷ (900-700) ≈ 114m ³, actual selection of 120m ³ to cope with pipeline losses.
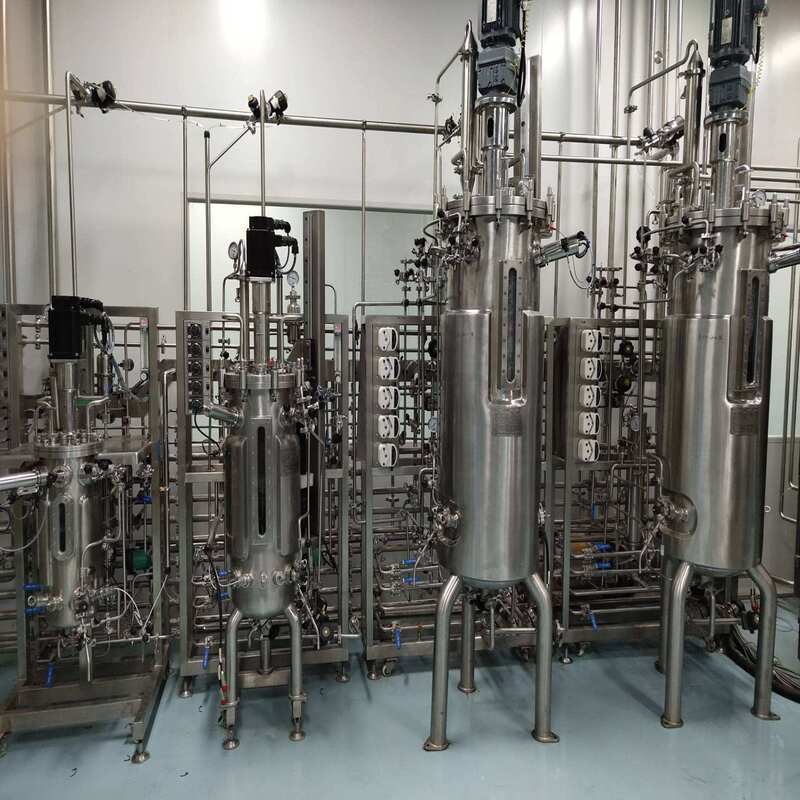
3、 Selection Decision
The final selection of gas storage tanks requires a closed-loop process of "parameter calculation → scenario verification → comprehensive weighing". For example, the selection process of a food processing plant can serve as a reference:
1. Basic parameters: The air compressor has a displacement of 8m ³/min, a pressure of 0.8MPa, and the gas equipment used is a filling machine (with moderate fluctuations);
2. Formula calculation: N=3, V=3 × 8 ÷ (0.8+1)=13.3m ³;
3. Scene adjustment: As it belongs to the food industry, the material selected is 304 stainless steel; Workshop height is limited, choose horizontal installation;
4. Final decision: 15m ³ horizontal stainless steel gas storage tank, equipped with DN65 interface, safety valve (with a popping pressure of 1.0MPa), and automatic drain valve.
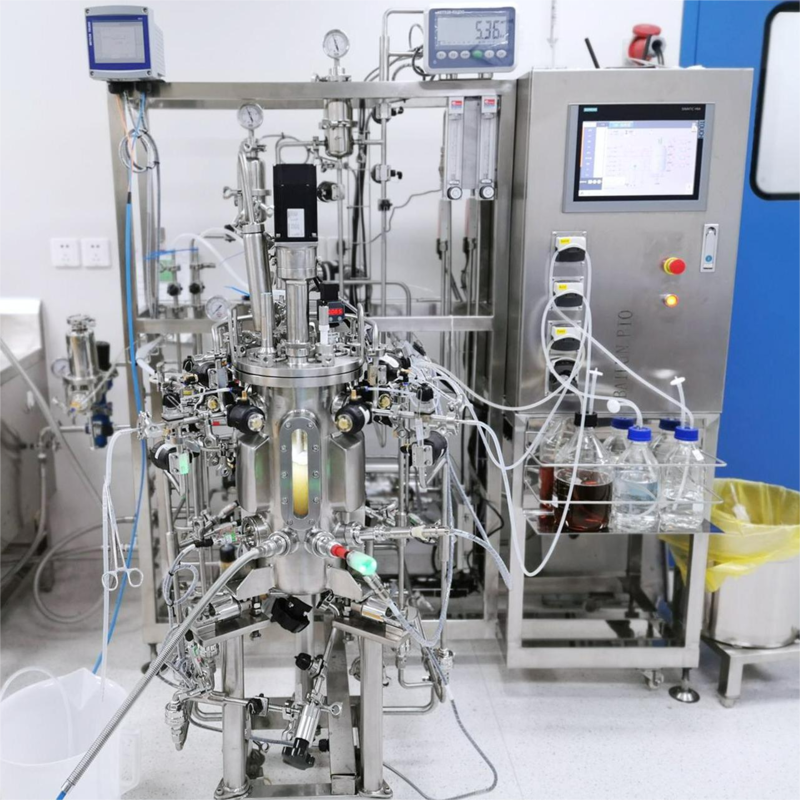
In short, the selection of gas storage tanks is an organic combination of scientific calculation and practical needs - it requires precise matching of system parameters and rooted in on-site working conditions. Only in this way can this "stabilizing reservoir" truly become the reliable cornerstone of compressed air systems.