Bailun has fully implemented 8 product production lines! From fertilizers to medical aesthetics! How many have you used?
The application of AI in biological response scenarios is not simply a combination of technology, but rather a closed loop of "data perception time modeling mechanism fusion automatic execution", which transforms the traditional experience driven production mode into an intelligent paradigm driven by data and algorithms, ultimately achieving a leap from "manual duty" to "autonomous optimization".
一、 Building an intelligent perception and control architecture with software and hardware collaboration
1. Hardware level: By deploying multi-dimensional sensors (such as temperature, pH value, dissolved oxygen, material flow rate, etc.), hundreds of dynamic parameter paths during the production process can be collected in real time.
The sensor network covers key production equipment such as fermentation tanks, reaction vessels, etc., ensuring real-time mapping between the physical world and the digital world.
2. Software level: Build an "AI intelligent brain" based on transfer learning and physical mechanism models, integrate historical production data (such as process parameters), and construct an algorithm framework with predictive and decision-making capabilities.
Software is linked with hardware devices through instruction interfaces to achieve automated control (such as device start stop and parameter adjustment).
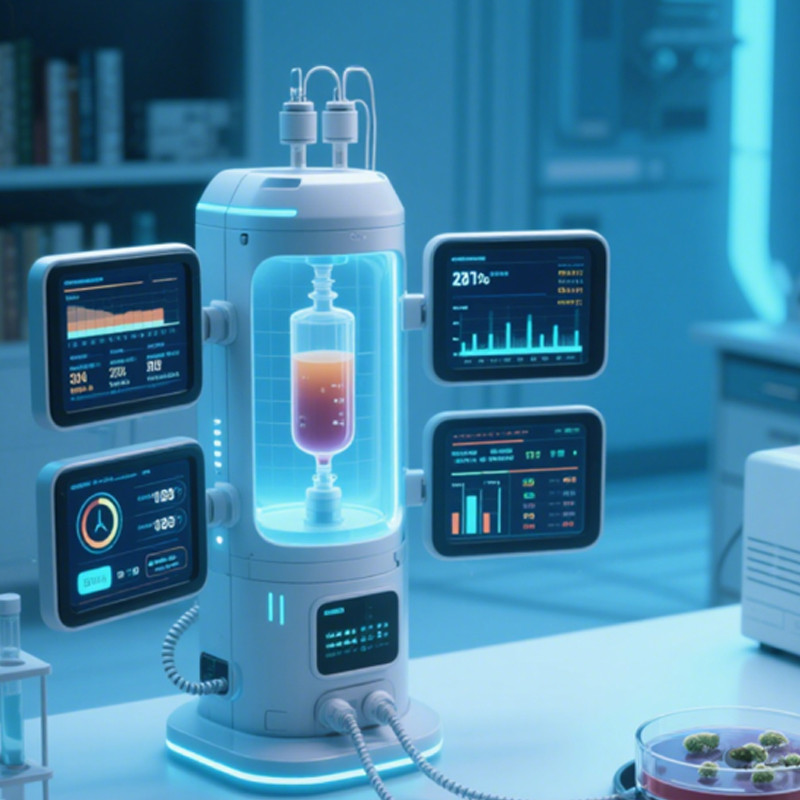
二、 Introducing a dynamic optimization mechanism with a time dimension
1. Full cycle time series prediction: Taking the "time dimension" as the core variable, AI generates the optimal operation plan for the future full cycle (such as fermentation process from the 20th hour to the 150th hour) at a millisecond speed based on the current production status, covering material ratio, temperature control, ventilation adjustment and other links.
2. Real time feedback and regulation: By continuously receiving sensor data, dynamically correcting the prediction model, predicting production trends and potential risks in advance, achieving a closed-loop control of "prediction execution feedback optimization", and minimizing production errors.
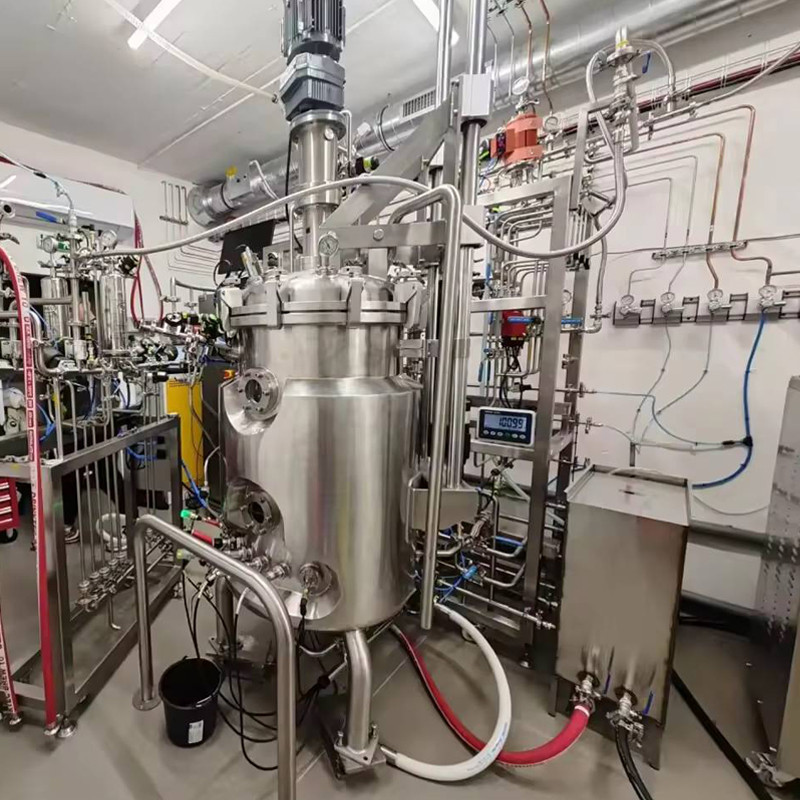
三、 Integration of data-driven intelligent decision-making and physical interpretability
1. Small sample learning and transfer learning: Breaking through the traditional AI's dependence on massive data, such as requiring only 5% of traditional data, combined with transfer learning technology, quickly adapting to new production scenarios, and reducing model training costs.
2. Physical mechanism empowerment algorithm: By embedding the physical laws of the production process (such as microbial growth kinetics and chemical reaction thermodynamics), the "algorithm black box" problem is reduced, making AI decisions have causal logic interpretability, and easy for operators to understand and intervene.
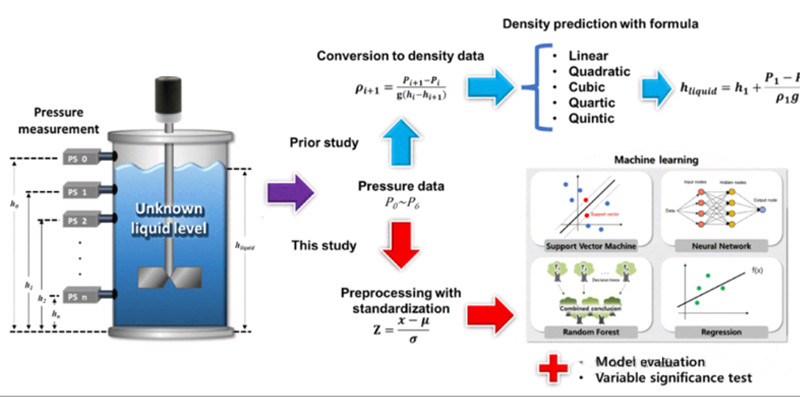
四、 Engineering implementation of cost optimization and efficiency improvement
1. The transformation logic of "model defined production": upgrading the traditional "process standardization" production mode to a "dynamic intelligence" mode through AI, with the core being the real-time optimization of production parameters driven by algorithm models, rather than fixed process execution.
2. Dual improvement of production capacity and stability: AI accurately regulates the growth environment or production process parameters of microorganisms, fully unleashing the potential of production capacity (such as increasing yield by 10% -20%), while ensuring product stability and reducing the risk of fluctuations caused by manual intervention.